Supplier Audits Explained — and How To Know If They're Right For Your Business
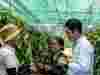
SUPPLIER AUDITS CAN BE A HELPFUL WAY TO FORMALISE YOUR RESTAURANT’S VALUES AND STANDARDS — BUT ARE THEY ALWAYS NEEDED? IN THIS ARTICLE, WE LOOK AT THE BENEFITS AND POTENTIAL PITFALLS, WITH REAL-WORLD INSIGHTS FROM BUSINESSES IN OUR NETWORK.
What are supplier audits?
A supplier audit is a document that evaluates and assesses a company's suppliers to ensure they meet specific ethical, quality and/or compliance standards. For restaurants and other hospitality businesses, these audits might cover areas like quality control, environmental sustainability, ethical business practices, food safety and regulatory compliance.
Where sustainability is concerned, they’re often designed to assess whether the supplier is in compliance with relevant legislation and/or with your own policies and standards in terms of environmental impact, social sustainability and ethical business practices throughout the supply chain.
Supplier audits in action
Seyha In is the Impact Manager at Rosewood Phnom Penh, Cambodia. She tells us that completing audits is one of their requirements for suppliers, especially when it comes to quality assurance and regulation compliance. “We use audits to check food safety and hygiene; quality of products (including production facilities); the standards for which the company applies; and sustainability and ethics.”
Meanwhile, at UK-based pub group Hall & Woodhouse, their audit is designed to ensure the appropriate treatment of the people who work for their suppliers. “It came out of an audit that a customer undertook on us, which was focused around ensuring we treated our team properly, and we found the experience to be very positive,” says Jon Mead, Innovation Manager. “With integrity being one of our values, we decided to adopt a similar process so we could ensure that those that worked for our suppliers were well looked after.”
The Hall & Woodhouse audit includes questions around freedom of choice, freedom of association, working hours and practices, living wages, working conditions and discrimination. Importantly, “The audit also includes a sub-set of questions which we ask a supplier’s employee directly, without the employer present,” says Jon.
What are the benefits of supplier audits?
PEACE OF MIND
Supplier audits can provide peace of mind, confirming that you’re working only with suppliers who have the same values and standards as you do — whether that means guaranteeing a certain level of quality, eliminating single-use plastics or ensuring your supply chain is free from human rights abuses. As environmental legislation becomes increasingly stringent, they can also help to identify and eliminate areas of potential risk. For example, having audits in place to ensure your supply chain is free from deforestation will make it easier to ensure your own compliance with the EUDR.
TRANSPARENCY AND ACCOUNTABILITY
As with any sustainability work, having processes and documentation in place helps to create greater transparency. Supplier audits provide clarity on your standards around quality, sustainability and/or ethical business practices, demanding greater accountability in your supply chain.
Having this documentation to hand can also be useful in tackling further sustainability efforts — for example, the Hall & Woodhouse audit functioned as supporting evidence when the team was going through their Food Made Good Standard evaluation. “Our audit helped us to prove the importance of human rights and positive employment practices, both for our own team and for those working for our suppliers.”
IMPROVED COMMUNICATION
Increased transparency across your supply chain and better visibility into the operations of your suppliers makes for an open exchange of information, improving your supplier relationships and making it easier to ensure your goals are aligned. “We already had excellent relationships with the majority of our suppliers, so it is good to be able to endorse their labour practices,” says Jon. “Our audit enables a better dialogue with our suppliers, and gives us the assurance that we are partnering with the right people.”
Sustainability audits also give you a firm foundation for communicating your sustainability work to your customers in credible, evidence-driven ways.
STRIVING FOR IMPROVEMENT
Supplier audits can create a ripple effect of continuous improvement across your supply chain. Seyha shares that the Rosewood’s audits have even brought in more business for their suppliers, as other F&B businesses have sat up and taken notice. “It is really beneficial for our business — not only for us, but for our suppliers themselves,” says Seyha. “Our audit lets us see what they do and how they do it. This allows us to understand their processes and provide feedback about what we encounter with their product. We can make recommendations for how they can do things better to meet our standards and improve for themselves, too.”
What sort of challenges are involved?
The main concern is to ensure that any audits you put in place serve a real purpose and provide valuable, useful information. Don’t put an audit in place just for the sake of it, and don’t require so much information that you find yourself drowning in unnecessary data; make sure the questions you’re asking are meaningful and standardised. Is each question truly worth asking — and does the person you’re asking have access to the answers? Just like restaurants, most farmers and producers are squeezed for time and don’t always have the resources to be completing extra paperwork, so it’s important to use their time — and yours — wisely.
“While the concept and purpose was readily accepted, and good relationships with suppliers were already established, time has been a challenge,” says Jon. “The expectation was that we would not have partnered with a business that undertakes unscrupulous employment practices, but we felt it was important to be able to prove this — and this takes time, both at our end and for the supplier.”
Sometimes it’s about striking a balance. “We focus on local produce, and this can be challenging as there are not many regulations from the government,” says Seyha. “International standards are costly for local suppliers in Cambodia to apply. This means we’ve had to adjust our criteria to make sure they are both achievable for the supplier and acceptable for us as the customer.”
How can I go about creating a supplier audit?
Once you’ve established that there is a need for an audit in your business for a particular focus area, you should clarify exactly what it is you need to know and write clear questions that will give you that information — no more, no less.
There are resources available that can help in the process; Jon shares that the design of their Hall & Woodhouse audits used the Ethical Trading Initiative base code. (Creating your audits is also something with which our team at The SRA can help!)
At Rosewood Phnom Penh, for each audit, they started by classifying their suppliers according to risk levels. “We established criteria and a frequency of audit for each risk level,” says Seyha. “The audit team includes representation from finance and purchasing, food safety inspectors and the culinary team.”
The finer details of supplier audits vary depending on the types of businesses and products involved and which metrics are important to you, but below you’ll find a generalised overview of what’s entailed.
How to conduct a supplier audit
- Define the objectives. Be crystal-clear about what you want your audit to achieve. Clear objectives will guide the entire audit process, ensuring it remains focused and provides meaningful data.
- Develop an audit plan. Your plan should define the scope of the audit, outlining the areas it will cover and the methodology that will be used (for example, providing an online question set, reviewing particular documentation, holding interviews, conducting site visits or some combination of the above.) You should also include details of when the audit will be carried out (e.g., annually, or before a new contract is signed) and who is responsible for conducting the audit.
- Build your audit. Add only questions that provide the necessary information for meeting your objectives.
- Inform your suppliers. Notify them of your audit process, giving them adequate time to prepare, gather documentation, etc.
- Conduct the audit itself.
- Collect your findings. Accurate documentation is important, as it makes the entire process meaningful and worthwhile. Include both positive and negative findings.
- Prepare an audit report. Compile your findings into a clear, concise report, including recommendations for improvement where necessary. Send this to the supplier to serve as a formal record of the audit.
- Outline necessary action. Follow up with your supplier to discuss the findings of the report, ask for their feedback, and agree on any necessary corrective actions, putting timelines in place.
For more advice, insights and stories from our team at The SRA and the businesses across our global network, follow us on Instagram and LinkedIn and sign up to our newsletter!
Our Projects & Consultancy team can offer support on creating supplier audits for greater sustainability in your supply chain. If you’re interested, drop Isabel a line at isabel@thesra.org.